Discover how plastic extrusion boosts production efficiency
Discover how plastic extrusion boosts production efficiency
Blog Article
Secret Advantages and Considerations of Implementing Plastic Extrusion in Your Jobs
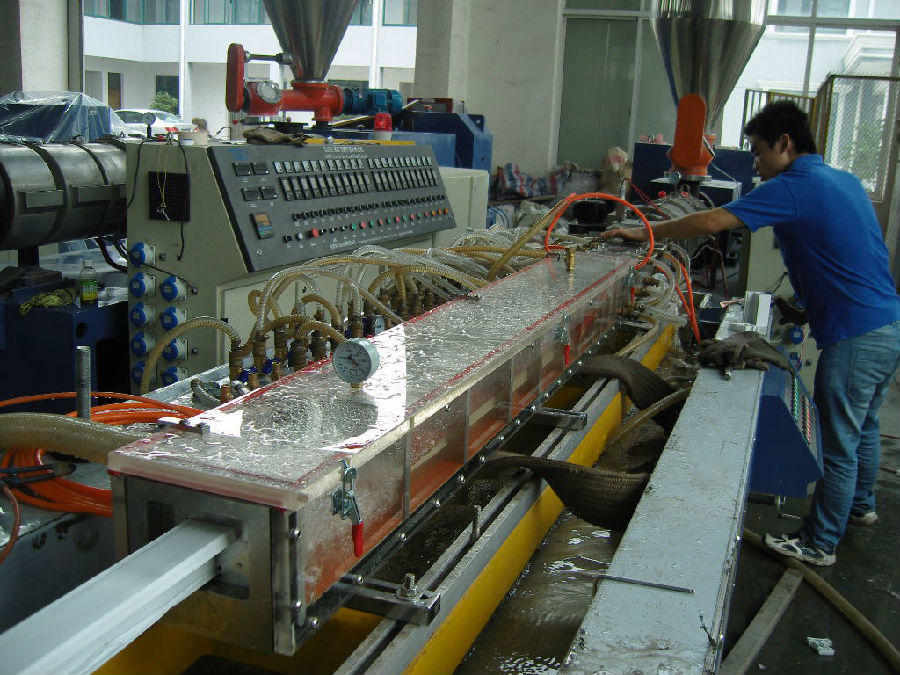
Comprehending the Basics of Plastic Extrusion
Plastic extrusion, a staple in the manufacturing industry, is a procedure that entails melting raw plastic product and reshaping it into a continual account. This profile, once cooled down, can be reduced into desired sizes or curled for later use. The beauty of plastic extrusion depends on its convenience. A large range of products, from piping to window structures, can be created. The process calls for an extruder, a complex device with a heated barrel, a revolving screw, and a die at the end. The plastic material, in the kind of pellets, is fed right into the extruder, where it's melted and compelled with the die, taking its shape. The selection of plastic and the style of the die identify the item's qualities.

The Economic Advantage of Plastic Extrusion
The economic benefit of plastic extrusion lies mainly in 2 areas: cost-efficient material production and beneficial production rates. With plastic extrusion, businesses can create high quantities of product at a reduced cost compared to various other methods. The process boasts an excellent production speed, considerably minimizing time and more enhancing its economic practicality.
Economical Product Manufacturing
A substantial advantage of plastic extrusion is its remarkable cost-effectiveness. This manufacturing process permits continuous, high-volume production with very little waste, which equates right into lower expenses. The raw materials utilized, normally plastic pellets, are reasonably inexpensive compared to various other materials (plastic extrusion). The procedure itself calls for much less energy than many various other production methods, even more reducing costs. Additionally, the extrusion process allows for a high level of accuracy fit the plastic, minimizing the requirement for expensive post-production modifications or adjustments. Furthermore, the longevity and longevity of extruded plastic items usually suggest much less need for substitutes, adding to long-lasting savings. All these aspects make plastic extrusion an extremely economical selection for lots of projects, offering an eye-catching balance in between expense and performance.
Beneficial Manufacturing Speeds
While maintaining the cost-effectiveness of the products, another notable benefit of plastic extrusion hinges on its quick production speeds. This performance in the manufacturing procedure is connected to the constant nature of the extrusion procedure, enabling high-volume production in a reasonably short time span. The rate of production directly associates to a decrease in labor expenses and a boost in result, thus boosting the total economic stability of the process. Additionally, the busy production does not compromise the high quality of the last product, making certain dependable and constant results. This mix of cost-effectiveness, high quality, and speed highlights the considerable financial benefit of applying plastic extrusion in numerous tasks.
Adaptability and Personalization: The Staminas of Plastic Extrusion
One of the prominent toughness of plastic extrusion hinges on its flexibility and personalization potential. These top qualities unlock to limitless design opportunities, providing producers the capacity to customize products to details requirements. This heightened degree of personalization not only boosts product capability however additionally substantially increases item uniqueness.
Unlimited Layout Possibilities
Plastic extrusion shines in its ability to use nearly unlimited style opportunities. Plastic extrusion can take care of a range of plastic types, expanding its application extent. With plastic extrusion, the style opportunities are essentially unlimited.
Boosting Item Originality
The adaptability of plastic extrusion can considerably boost item originality. This process permits developers to explore different shapes, sizes, and colors, providing them the flexibility to create unique items that attract attention in the market. It is this personalization that offers a distinct identity to each product, differentiating it from its rivals.
In addition to its visual advantages, check these guys out the customizability of plastic extrusion also provides functional advantages. Therefore, plastic extrusion not only enhances item individuality however additionally its energy and marketability.
Layout Limitations in Plastic Extrusion: What You Need to Know
How can create restrictions potentially influence the procedure of plastic extrusion? While plastic extrusion is flexible, layout constraints can cut its benefits. Certain complex layouts might not be viable because of the restrictions of the extrusion procedure, possibly her comment is here limiting the development of intricate profiles. The procedure is much less appropriate for multi-chambered or hollow frameworks. In addition, the extrusion process might not always supply the desired surface area coating, particularly for those requiring high gloss or optical quality. Product option can additionally present obstacles, as not all polymers are suitable for extrusion. High-temperature resistant plastics, for circumstances, may provide troubles. Understanding these restraints is essential for efficient application of plastic extrusion in your projects. plastic extrusion.
Reviewing the Ecological Effect of Plastic Extrusion
While understanding design constraints is a substantial element of plastic extrusion, it is equally essential to consider its ecological ramifications. The procedure of plastic extrusion involves melting plastic materials, potentially launching damaging gases into the atmosphere. Utilizing recycled plastic materials in the extrusion procedure can decrease ecological influence.
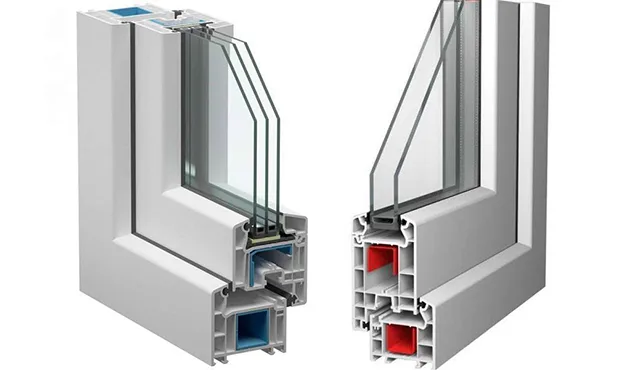
Study: Successful Projects Making Use Of Plastic Extrusion
Success stories in the area of plastic extrusion try this website abound, showing both the versatility and efficiency of this production process. plastic extrusion. One more effective situation is the manufacturing of plastic movie for product packaging and agriculture. These instances illustrate plastic extrusion's vital role in various markets, testifying to its versatility, cost-effectiveness, and dependable output.
Final thought
To conclude, plastic extrusion uses a effective and cost-effective technique for producing complex shapes with minimal waste. While it supplies many advantages such as cost-effectiveness and convenience, it's essential to think about prospective design restrictions and ecological results. Implementing naturally degradable or recycled products can alleviate these problems, boosting sustainability. Integrating plastic extrusion into projects can bring about effective outcomes, as evidenced by countless case studies.
Plastic extrusion, a staple in the manufacturing market, is a procedure that entails melting raw plastic material and reshaping it into a constant account. Plastic extrusion can handle a range of plastic kinds, broadening its application extent.How can create constraints potentially impact the procedure of plastic extrusion? The process of plastic extrusion includes melting plastic products, potentially launching unsafe gases right into the atmosphere. Utilizing recycled plastic materials in the extrusion process can minimize ecological effect.
Report this page